In the 1970s, due to the promotion of continuous ribbon dyeing and ironing machine, the processing of ribbon has developed from the traditional process of dyeing before weaving to weaving before dyeing, weaving before bleaching, ironing after processing, and the ribbon technology has entered the ranks of mechanized mass production. In the early 1980s, the industry introduced high-speed shuttleless loom, ironing machine, wrapping machine, warping machine, etc. from Switzerland, Italy and the Federal Republic of Germany, and the ribbon technology entered a new stage of development. The progress of webbing technology has brought about the upgrading of products. In 1980, the rubber ingot belt was developed, which has the characteristics of soft, light, thin, firm, small elongation, small impact force, short and flat joints.
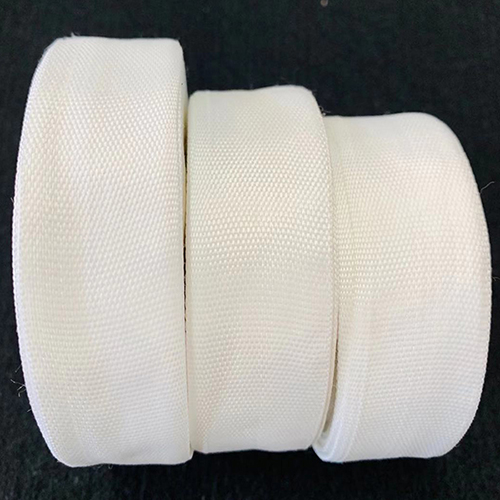
Cotton ribbon wholesale The progress of process technology has brought about the upgrading of edging webbing products. In 1979, the trial production of the domestic generation SD9-9 rubber ingot belt was successful, which ended the history of rubber ingot belt products relying on imports. After the weft tube is formed by the yarn warp cylinder and weft winding, it is inserted on the fixed gear seat of the knitting machine, and the weft tube rotates along the 8-shaped track to draw the yarns to cross weave with each other. Siping Customized Cotton ribbon Usually, the number of spindles is even, the woven tape is tubular, the number of spindles is odd, and the woven tape is flat. Spindle weaving technology has been applied since old China. The number of spindles varies from 9 to 100 due to different equipment.
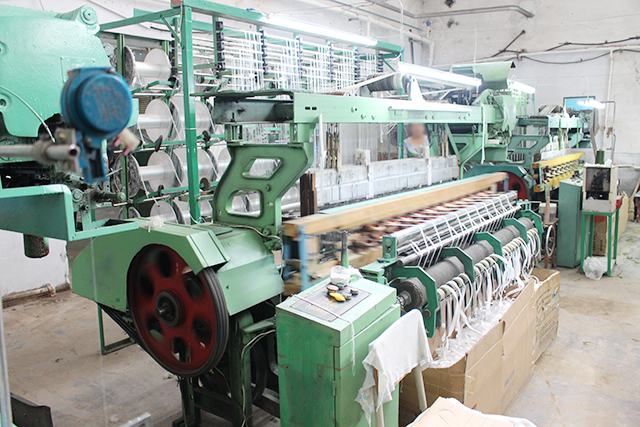
The basic process flow of knitting is: bleaching and dyeing - weft rolling - weaving - off machine cutting - packaging. Since 1960, many technical innovations have been carried out on the knitting machine, mainly including the enlargement of peach plate diameter, the installation of an automatic stop device for breaking rubber bands, and the replacement of iron ingots with nylon ingots. The improvement of these equipment has increased the vehicle speed to 160~190 rpm, doubled the stand rate and greatly improved the product quality. In 1980, SD-81A and B rubber ingot belts were developed, which are soft, light, thin, firm, with small elongation, small impact force, short and flat joints. At the beginning of 1990, the trial production of car seat belts for Santana cars was successful. After more than two years of research and trial production, the product quality reached QC49-92 and TL-VW470 standards.
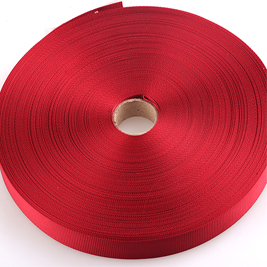
The longitude and latitude are interwoven. [Subject] After twisting, the yarn is warped into a bobbin (pan head), and the weft yarn is shaken into a bobbin, which is woven on the loom. In the 1930s, it was used for hand looms and iron wood looms. In the early 1960s, the 1511 loom was converted into a belt loom, which is still widely used. Due to the small width of the belt, the weaving methods are different, ranging from single, double, dozens of pieces, from single layer to double layer. In 1967, the research group of shuttleless weaving belt with workers as the main body in the industry successfully designed and manufactured a high-speed single shuttleless loom by itself, which realized that the weaving belt does not need shuttles, and the process is shortened, the floor area is small, and the labor productivity is improved, which is an innovation in the history of Chinese weaving belt technology.