Since the early 1930s, Backpack webbing All are handmade textile production, and the raw materials are cotton thread and hemp thread. After the founding of the People's Republic of China, the raw materials for ribbons have gradually developed to nylon, vinylon, polyester, polypropylene, spandex, viscose, etc., forming four major types of technology, namely weaving, knitting, knitting, jacquard, and the fabric structure includes plain weave, twill, satin, jacquard, double layer, multi-layer, tubular, etc. With the enhancement of economic strength, the development of backpack webbing is also advancing. The progress of webbing technology has brought about the upgrading of products.
We all know that the backpack ribbon is not literally understood when printed. Before printing, it was done in this way. First, the ribbon with the same thickness and width as the original version was customized according to the customer's requirements. After production, it needs to be ironed and leveled by the ironing machine, and then the packaging is 100/200 yards and each roll is folded (of course, it also depends on the actual situation of the customer's needs)
The supply of ribbon printing is divided into many printing processes, such as printing, heat transfer printing, hot pressing, silk screen printing, manual printing, etc.
In backpack ribbon printing, those with a thickness of 0.15-0.8MM are mostly used for silk screen printing, and those with a thickness of 0.15-0.8MM are usually used for hot pressing or manual printing. Of course, the printing effect varies according to customer needs.
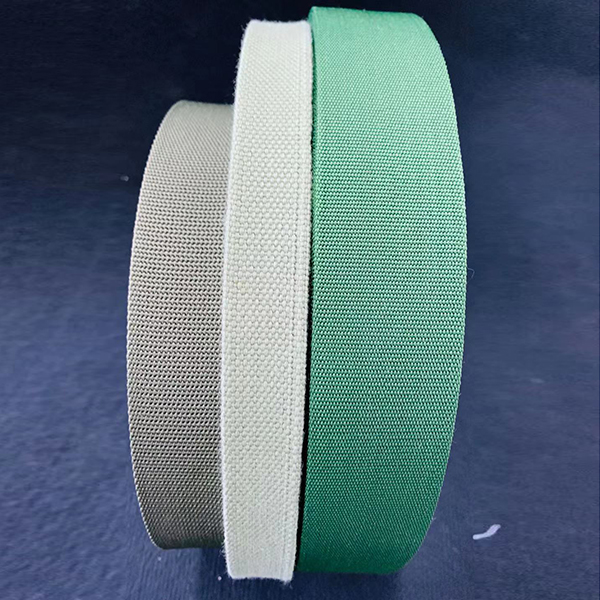